Often, we go through life not realizing there are obstacles that could easily be fixed with a bit of consideration and action. This seems to plague our thought patterns, seemingly “unavoidable” issues cropping up to add that extra bit of annoyance we really didn’t need that day. The BASK Bag from two-point is a direct response to this idea, solving the problem we didn’t know we had: The Tote.
The tote is a simple one pocket bag, usually cotton or canvas. You’ve probably interacted with at least a couple already today. Usually, an elegant solution for getting a small amount of items from point A to B. However, designers are carrying samples of wood, glass, or stone as well, all bouncing around at the bottom. This presents an issue for all personal items, as well as searching hands trying to find the right swatch. This pain point extends to materials such as fabric and paper, both easily becoming cumbersome and jumbled carrying multiple projects at once. Designer and founder of two-point, Jordan Cammarata, shares more behind this design in an exclusive interview with Design Milk.
What pain points within the design industry led you to the BASK Bag? Any specific experiences?
This bag was born out of my first project for BASK, expert furniture curators and providers. Brian and Adam reached out to me about a few custom projects within their new space, as well as a finish library. For anyone familiar with the finish selection process, it can be quite complicated. We started out not necessarily focusing on the object, but the process. During this discovery period, we were at a major manufacturer showroom for a meeting, and we all showed up with the ubiquitous single pocket tote bag. We’re all just dumping our single pocket tote bags onto the table with the different samples, and somehow organizing them into a finished palette. I said, “There’s a lot of brainpower here, we could probably design something better.” We designed the library itself, but also the means of transporting finishes to the various locations where the project is happening.
Were there some unexpected discoveries or challenges you encountered during the design process?
Like many design projects, where we started and ended was not what we had in mind. I had originally pitched a tray that folded, and was more or less a briefcase. I went down the rabbit hole with what this folding tray could look like, and realized a tray was ultimately not the right form factor. The more we thought about it, a bag lent itself to the right solution. Bags are generally lightweight. If they’re constructed correctly, you can make something quite strong, and relatively affordable as well. Sandra, she’s the interior designer, said “The samples are sharp, you might have a piece of glass snag on a jacket.” She recommended, “Why don’t we add some flaps to protect the contents and add some rigidity?” Before you know it, we had we added the flaps to our model. She also mentioned that all the designers on the interiors team carried around a white tablecloth. At a client meeting, there would be a wood table or some sort of dark surface, and you wanted to be able to lay out a blank canvas for your swatches. This eventually led us to the mat design. It’s soft goods, it’s lightweight, and now you have that blank canvas. That was an a-ha moment for us. I’m not the hero here, one of my favorite things about two-point is the collaboration.
Design samples are relatively heavy, some packs solely include concrete and stone. How did this consideration affect the final design?
We didn’t want to solve for every use case with the BASK Bag. We wanted to solve for a very specific moment in the design process, and account for maybe 90% of the use places within that snapshot. In our research, we found that often a client is given a curated list. From hundreds of options, they’ll shortlist and present to the client digitally. They might whittle that down to three, and then go to the client meeting. We really tried to focus on how that process actually goes, and designed for a more curated list of finishes, not a bag that can hold 100 pounds. The center gusset was meant to be open and the deepest pocket so that you could store large carpet samples, or a wood plank. There are handles integrated into the flaps, and the shoulder strap is meant to distribute heavier weights perfectly.
How does your background influence your process, and the finished product?
I originally went to Business School, dropped out, discovered industrial design, and kind of started over. Most of my friends that I went to high school with that went through four year programs were just finishing at that time. I really lucked out being right hand to a designer in New Hope, interning for four years. Post graduation, I worked for all types of companies, from designer roles to bills and account executive roles to production management roles. At the end of the day, whatever you’re designing needs to get manufactured. It has to be produced at a price point where you can ultimately sell that to your target customer at a price that they’re willing to pay, all the while not stifling the design process. Those constraints can kill ideas at the very early stages in the process. That’s why it’s amazing to be in Los Angeles, where you have such an amazing design community. You can really get anything made here relatively affordably and quickly. It’s a combination of experience and collaboration, and being part of this vibrant manufacturing scene.
Your studio, two-point, launched in 2023 – are there any takeaways you can share on that experience after sharpening your skills in the industry?
The studio happened organically – you learn along the way. I didn’t necessarily have a plan, but I did have relationships and people that I’ve been working with in the industry for over 10 years. I started taking meetings and coffees, and seeing what people are working on. Ultimately, Brian and Adam from BASK were gracious enough to extend an invite to participate in their new office. That first project really catalyzed the entire business, and I learned that there’s actually a greater need in our industry for a very specific type of custom product design firm. One that bridges the gap between the two points, where we get our name. Whether it’s a business person or a designer working with a manufacturer, it can be kind of a clunky conversation. Very engineering heavy, ‘let’s get it done’ type of talk. That was really the genesis of the company. I’m generally saying yes to projects that other people say no to, so they’re one off things that need to be designed. I’m loving these smaller pieces. I’m also interested in growing and scaling, and we’re competing on some larger projects. Excited to take on bigger work, to take on employees. We’re trying to grow organically, not too fast, and in the right ways. It’s super fun, and I’m loving the process so far.
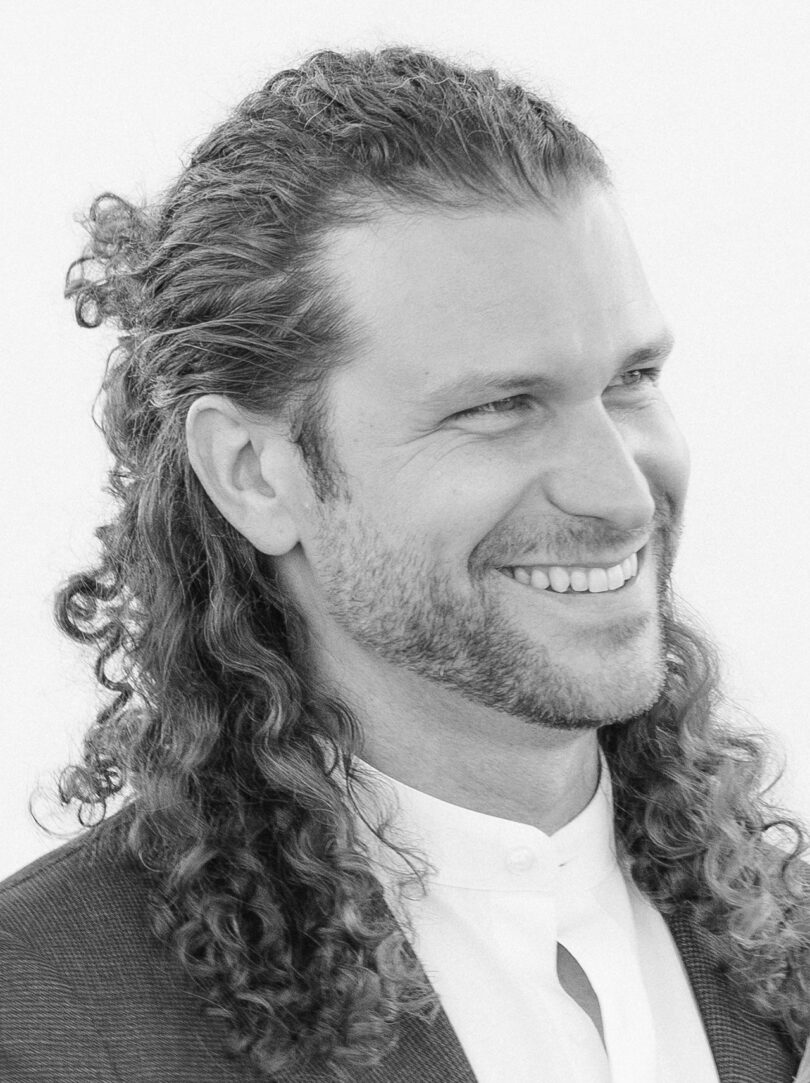
Jordan Cammarata
For more on the BASK Bag, click here. To learn more on two-point, visit their website here. For updates on BASK, click here.